Who are the winners of the Dutch Design Awards? What drives them and what is their vision of design? This time in the Winner’s Portrait series are Peter van de Water and Sarah Schiffer. Together they developed the Gispen Sett CE bank, he as designer and she as concept manager at Gispen. Their efforts resulted in a Dutch Design Award in the category Product.
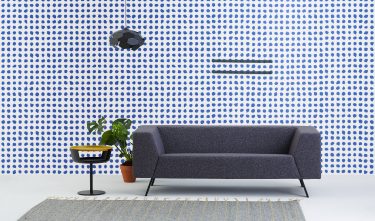
You produce several circular furniture items, so why did you choose to submit the Sett CE sofa?
Sarah: ‘The Sett CE was scouted, but we would have submitted it ourselves anyway. It is a timeless design and the most circular product we make. And it has taken four years. In order to achieve circular production, we use a design framework that includes a checklist listing various focus points. The Sett CE sofa has been improved in terms of circularity on every front. Ticking every single box is not quite yet possible. It is always a question of making choices.’
The sofa does not scream sustainability, but the reuse of materials is actually subtly incorporated into the design. Was this a conscious decision?
Sarah: ‘That does seem to be the case with this sofa, but the Sett CE bank is an existing design that we have reproduced. We have changed nothing in its appearance, with the exception of adding a hatch behind which the printed frame and recycled foam are visible. The invisibility of circularity is not an objective in its own right for us. In fact, I would rather it was visible. There is still a lot to be done in our industry when it comes to awareness.’
Peter: ‘Sustainability seems to be the new standard for many people. Logical, as consumers have little insight into the intensive processes of change that are needed in business operations in order to produce in a circular way. Circularity is still far from standard in this industry. Making sustainability visible is therefore still very important. Many products are good and sustainable, but if you don’t know, you cannot make an informed choice.’
What are your greatest challenges in terms of circular production?
Sarah: ‘You cannot really produce in volume if you do not tackle every aspect of the organisation. The circular economy comprises so many different areas. You really have to be a serious expert if you want to fully understand how it works. It is therefore often the case that each customer asks a different part of the question. One customer, for instance, looks at the toxicity of fabrics, while another focuses more on reuse and the extension of life. The Sett CE sofa is a success, but applying all of these elements to every product is almost impossible. You can, for example, use biodegradable materials but this also means that the product has a shorter life expectancy. It is a question of constantly making choices, and that is complicated. On the other hand, circular entrepreneurship has a very good business model. Our circular clients are our best clients. And as we all have a shared goal to ensure that the furniture lasts as long as possible, we are continuously working together. As such, we have had to rethink our whole system in recent years, but it is more than worth it.’
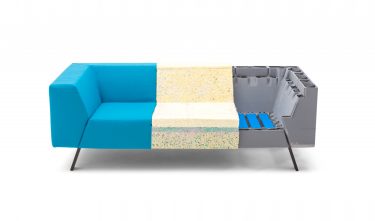
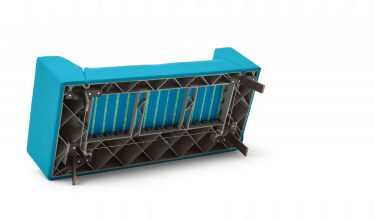
What does this demand from you as a designer, Peter?
Peter: ‘If you want to design circular products, you need knowledge. Not only about sustainable materials, but also about the whole chain. From raw materials to waste processing. Whereas function used to be the starting point for your design, you now have very different boundaries within which you have to be creative. This is challenging, but also nice. I find it interesting and have gathered a lot of knowledge that I am also keen to share with my customers. It also generates a new kind of motivation. As such, I am really able to contribute to a market with better alternatives. Now that I know much more about it, there’s no going back. I have included a commitment to sustainability in my contract with a new customer. This means that my customer also has to work on sustainability. It is actually a topic that now stands alongside other obligations such as sales and marketing. I am aware that I am now in a position to be able to do this, and that not every young designer dares make such demands, but this is how we, as designers, can set a standard.’
The jury was impressed by the workable, circular system for a consumer product on this scale and an example for the whole manufacturing industry. How far is this industry
Sarah: ‘One of the first things I learned when we started with this is that you cannot want everything at once. We are already quite far, but we cannot yet justify every single screw. We also do not know exactly where every bit of iron ore comes from, so to speak. We should not be afraid to share our insights and knowledge with parties you would perhaps not so easily come into contact with. We have to do it together.’
Peter: ‘We have a shared responsibility. I recently spoke about a commodity passport. If you can see exactly all the ingredients in a pot of peanut butter, then it should be the same for a piece of furniture. So that you can see straight away just how it should be recycled. Many companies are scared by this, because they then have to admit that things don’t always go perfectly. We really should be a lot more relaxed about this. Circularity is still very much in its ‘development’ phase. And that’s a good thing. You should be allowed to make mistakes. The most important thing is that you do something, begin somewhere.’
Circular sofa
The Sett CE bank by Gispen is made from 95 per cent recycled materials. In order to combat plastic waste, Gispen uses its own discarded plastic. Together with TU Delft, Searious Business, Marcel van Galen Design and Wittenburg, a new raw material is generated from the waste material and the body of the sofa is then printed by 10XL. This can be reused up to ten times without any new material being added. The seat and back of the sofa are made from recycled polyether foam. All materials in the Sett CE can be separated out and innovative techniques mean that each component can be processed into a new product.